Download Full Press Release here
Disclaimer: The views expressed herein by the authors in no way reflect the official opinion of the European Space Agency.Orion Additive Manufacturing, a Berlin based startup focusing on making advanced 3D printing systems accessible for aerospace applications, today announced the launch of their A150, an Industrial Additive Manufacturing System for high-performance polymers 𑁋 The A150 utilizes patent-pending Thermal Radiation Heating to 3D print parts using aerospace-grade materials that are comparable to injection molded parts in strength. The 3D printing system was designed and optimized specifically for printing with high-performance polymers, like PEEK, ULTEM and PPSU to produce components suitable for aerospace and a wide range of other applications.
Learn more about Orion AM
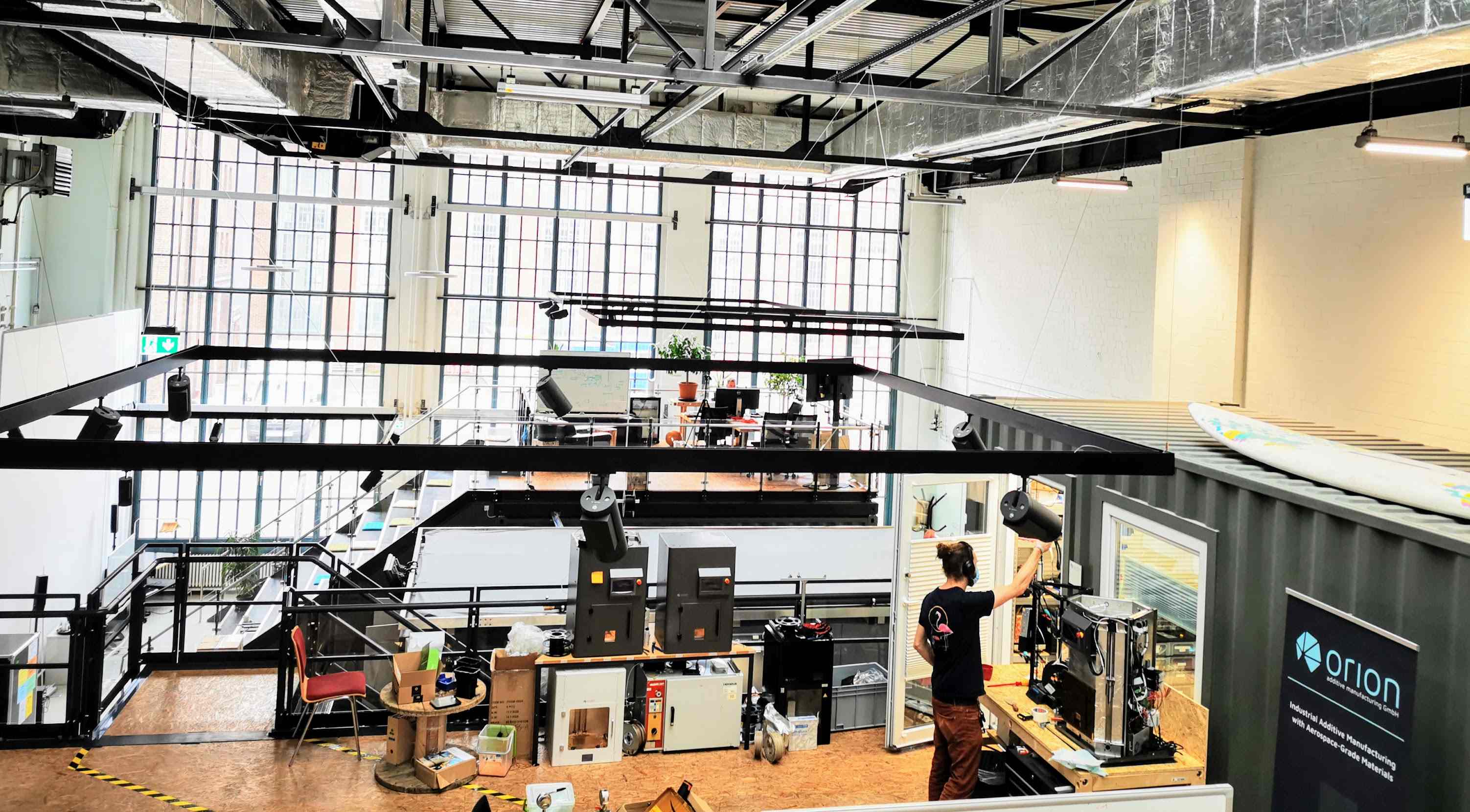